Oh, I have learned so much the past couple months. This post is no exception. Remember the "easter egg scarf"? I know - you're tired of me talking about it. Well, I decided to over dye it.
(Warning: may be boring for those who do not want to learn about the fine points of protein fiber dyeing.)
Thankfully, I had some left over yarn that I had used to weave the scarf.
I made little bundles of fiber out of the leftover bobbins to see what would happen to the already colored fiber.
So I mixed a few dye pots with different colors to test what would happen to each color. Always do test swatches so that you know what will happen to the scarf. No need to put the setting agent into dye pot since there's no need for it to set. Just a little dye and hot water to dissolve it will be enough to get a test dye pot to dip into.
The goal was to get it to look like this (the third from the left, above).
Except I made one glaring mistake.
I really wanted to get a "cool" shot for the blog. Except it took me a good minute to find my camera, take off my gloves, and take the picture:
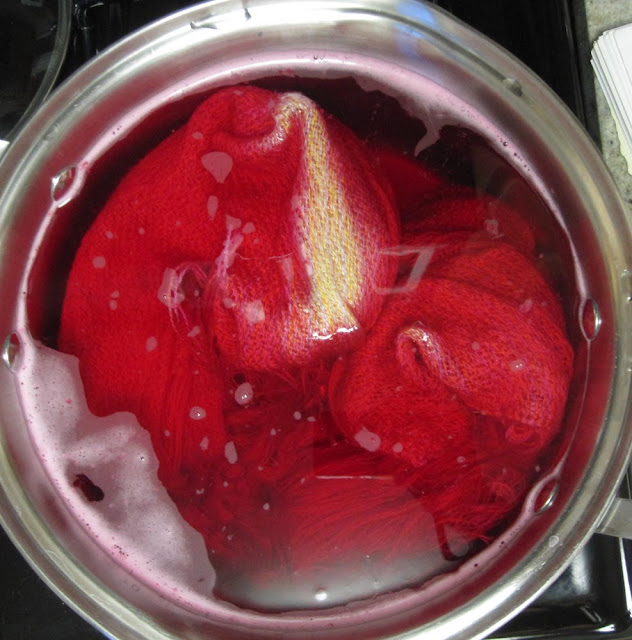
Can you guess what happened? Yep, I had this huge area that didn't get dyed. And I wasn't able to stir the pot either, so the entire scarf was just strangely streaked - and not in a good way.
And if you have such a little amount of dye in the pot, it takes very little time for the fiber to soak it up. It took maybe 4 minutes for the dye to disappear.
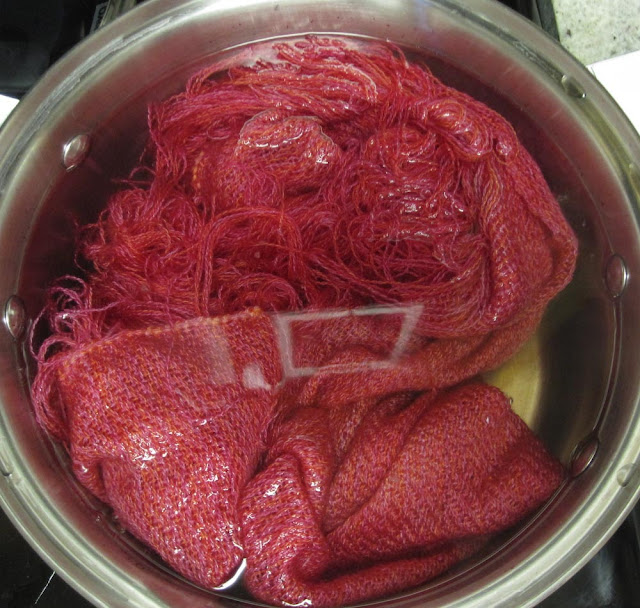
So I had to add about 3 times the amount of dye that I really wanted to add in order to get something that looked okay. And practically burned my hand off in the process.
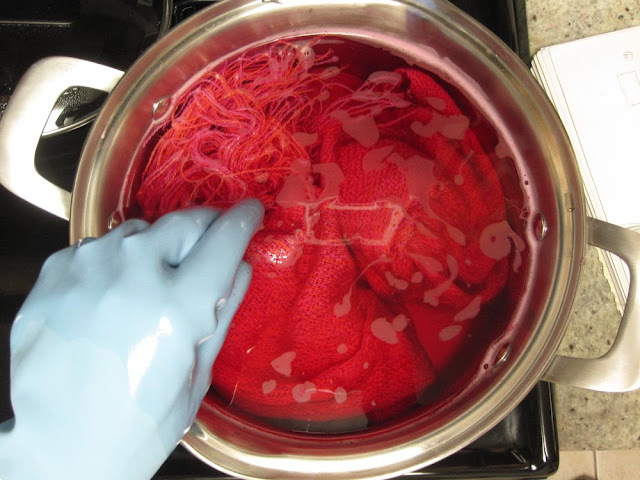
Either way, it still came out beautiful. Just not quite the colors I thought. Oh well. Next time!
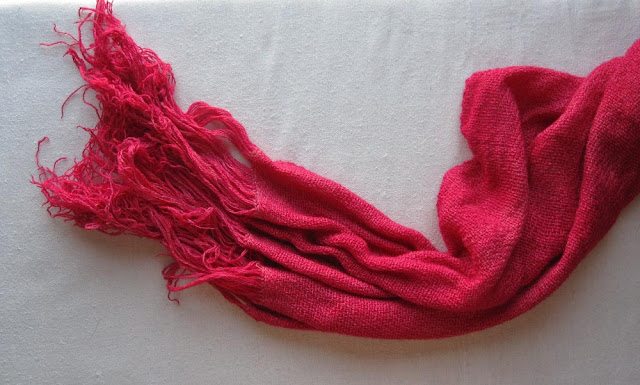
What I learned and want to pass on to other newbie dyers:
1.) Always do a dye swatch test to see what will happen when you over dye. I was very unsure what the yellow would do when I added it to the fuchsia and brick red dye pots. After I did swatches, I knew!
2.) Have a large enough dye pot. There is something to be said to have the fiber "swimming" around freely. Do not skimp in this. Find old pots at Goodwill stores or if you have a friend who cans their own food you might be able to score an old large pot! The pots I currently have are not big enough for dyeing fabric. It's fine for my warps (think warp = 1/2 the amount of fiber than the fabric it makes). The last time I went to Reny's (best savings store ever - a Maine institution), I wanted to find a $20 lobster pot but since it was the end of summer, all the pots had already been snatched up for their intended use. Next time, Reny's!!!
3.) When dyeing any sort of protein fiber - that is an acid dye using heat - the minute it hits the dye bath is what the object will look like, so be especially careful with small amounts of dye. If you don't submerge evenly and start stirring right off the bat, you might get splotchy coverage.
4.) Even though rubber gloves feel like they are insulating you from a boiling pot of water - um, I don't need to finish that one, do I?
5.) Be prepared with the camera, if you're documenting. Or have someone else do it for you. Don't let your ego get in the way. The craft should come first!